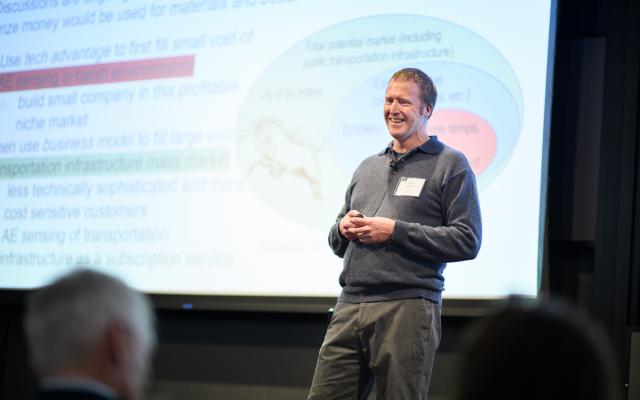
Ultrasonic acoustic emissions (AEs), typically in the frequency range of 100 kHz to 1 MHz, can be spontaneously generated in solid materials as stress energy is released when destructive changes to the material structure occurs, for example material fatigue due to a cyclic load. Catastrophic structural failure can be predicted, under service conditions, by passively sensing AEs and analysing them. AE sensing is one of the major techniques used for Structural Health Monitoring (SHM), an umbrella term for the set of technologies that allow us to keep an eye on the condition of infrastructure, to help prioritize maintenance and keep our commutes safe. The state of the art in AE sensing is to use a piezoelectric crystal as the transducing element of a sensor to convert the acoustic wave to an electronic signal. The sensitivity of piezoelectric crystals depends strongly on the acoustic frequency, with a narrow maximum at the resonance frequency of the crystal. To avoid signal distortion due to frequency-dependent sensitivity, the crystal can be tuned to a resonant frequency much above the acoustic-emission frequency range, but this mode of operation has a significantly reduced sensitivity. Piezoelectric crystals have a limited temperature range of operation, with an upper limit of about 400℉, and they are also susceptible to irreversible transduction-performance degradation by neutron irradiation. There is therefore a need for a better AE sensor that has high and frequency-independent sensitivity, which is beneficial for all applications, and that tolerates extreme temperatures for space, combustion and chemical-processing applications and neutron fluxes in nuclear environments.